1. Basic Principle
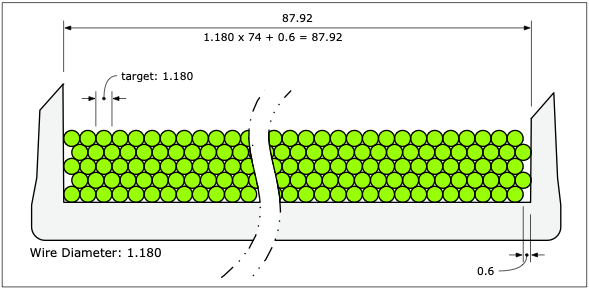
Width = (wire diameter x lap count) + radius of wire
- At the last lap to the wall, left space should be the half of wire diameter.
- Wire laid on the between wire laps on next layer.
- The wall on both side should be straight up to maintain same space.
- The problems come out the wire diameter variates.
1.1 Failed Case of smaller diameter than target diameter.
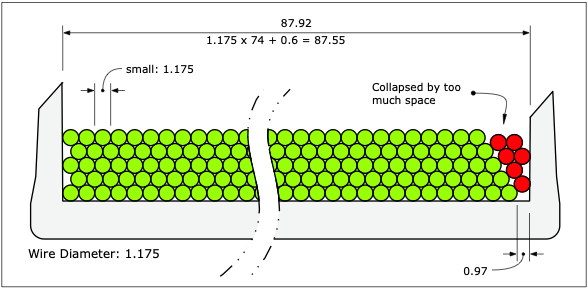
- Cause of die wear at the drawing, the diameter of wire variates.
- Because of too much space at the last lap, un-even level area becomes wider as layer added.
- To prevent this problem, operator stop the machine and adjust the distance of last lap by hitting the wire.
- The possibility of reverse winding goes up, resulting low productivity.
1.2 Failed case of bigger diameter than target diameter.
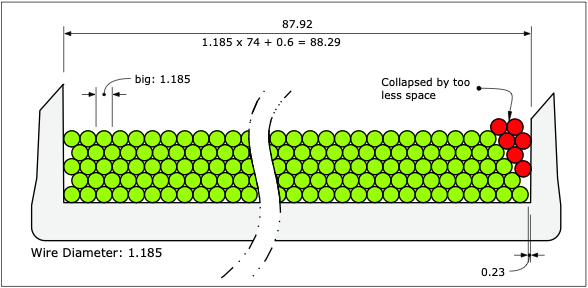
- The wire diameter becomes bigger as die wear out.
- As a result, there is no space to layer on next layer to the wall
- Then wire goes next furrow between bottom wires and start to ruin the principle
- To keep the principle, operator try to push wire to the wall by stick, however the failure rate goes up effecting winding productivity.
**Ref. Ways to make the Level Layer Winding
Comparison Item | By Operator | Apply Grooved Spool | Introduce Full Automatic M/C |
---|---|---|---|
Invest Costs | None | Spool Mould | Automatic M/C |
Method | Operator use wood or plastic stick to arrange the last distance. To do this, need to stop the machine. | Grooved Spool covers a wire diameter variation, so do not need to stop the machine. | Machine calculate the wire diameter during first layer and adjust the distance before wire arrive. |
Productivity | Extremely Low | High | Known High |
Benefits | No Investment, good for small production. | One operator can run 2 machine with small investment. | Need more space and investment costs, also need expensive spool material. |
Manufacturer | - | Bogang Precision Co. | Gimax s.r.l & Lamnea Bruk |